What is Machine Vision?
Machine vision is the ability of a computer to see; it employs one or more video cameras, analog-to-digital conversion (ADC), and digital signal processing (DSP). The resulting data goes to a computer or robot controller. Machine vision is similar in terms of complexity to voice recognition technology.
Two important specifications in any vision system are sensitivity and resolution. Sensitivity is the ability of a machine to see in dim light or to detect weak impulses at invisible wavelengths. Resolution is the extent to which a machine can differentiate between objects.
In general, the better the resolution, the more confined the field of vision. Sensitivity and resolution are interdependent. All other factors held constant, increasing the sensitivity reduces the resolution, and improving the resolution reduces the sensitivity.
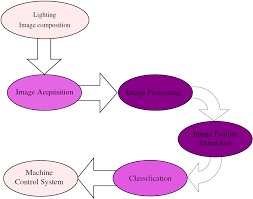
How does Machine Vision work?
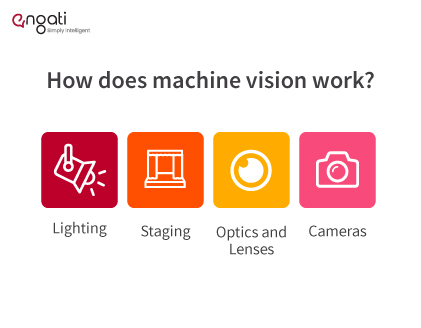
A machine vision system consists of several critical components, from the sensor (camera) that captures a picture for inspection, to the processing engine itself (vision appliance) that renders and communicates the result. For any machine vision system to work reliably and generate repeatable results, it is important to understand how these critical components interact.
1. Lighting
The human eye can see well over a wide range of lighting conditions, but a machine vision system is not as capable. You must therefore carefully light the part being inspected so that the machine vision system can clearly 'see' them.
The light must be regulated and constant so that the light changes seen by the machine vision system are due to changes in the parts being inspected and not changes in the light source.
You will want to select lighting that 'amplifies' the elements of the part that you want to inspect and 'attenuates' elements that you don't want to inspect. In the left picture, poor lighting makes it difficult to read the letters on this part. In the right picture, the lighting has been selected to clearly show the lettering.
Proper lighting makes inspection faster and more accurate. Poor lighting is a major cause of failure in machine vision inspection systems.
2. Staging
Staging, sometimes called fixturing, holds the part to be inspected at a precise location in front of the camera for a Vision Appliance to 'see'. Staging is required for three reasons:
- To ensure that the surface of the part that you want to inspect is facing the camera. In some cases the 'parts' may be rotated to inspect multiple surfaces.
- To hold the part still for the brief moment required for the camera to take a picture of the part.
- To speed up the processing by putting the part in a location known to the Vision Appliance.
3. Optics and Lenses
The lens gathers the light reflected (or transmitted) from the part being inspected, and forms an image in the camera sensor. The proper lens allows you to see the field-of-view you want and to place the camera at a convenient working distance from the part.
4. Cameras
The machine vision camera contains a sensor that converts light from the lens into electrical signals. These signals are digitized into an array of values called pixels and processed by a Vision Appliance™ to perform the inspection.
The resolution (precision) of the inspection depends upon the working distance, the field-of-view (FOV), and the number of physical pixels in the camera's sensor.
What are Applications of Machine Vision? What can Machine Vision do?
Machine vision systems are used in various industrial and medical applications. Examples of the use of machine vision solutions include:
- Electronic component analysis
- Signature identification
- Optical character recognition
- Handwriting recognition
- Object recognition
- Pattern recognition
- Materials inspection
- Currency inspection
- Medical image analysis
You also see the use of machine vision systems in meteorology, robotics, and several other fields.
What is the difference between computer vision and machine vision?
There are quite a few commonalities between computer vision and machine vision. Both technologies make use of image capture and analysis to carry out tasks with speed and accuracy human eyes can’t match. They both use an imaging device that contains an image sensor and a lens. Both use an image capture board or frame grabber, but in some digital cameras that have a modern interface, a frame grabber is not needed. Both computer vision as well as machine vision require application-appropriate lighting and both these technologies need software that can process the images through a computer or an internal system.
So, if you’re looking at machine vision vs computer vision, both of these technologies seem to be rather similar. The difference between these technologies is becoming rather blurred, but if you want a good distinction between them, you should look at their Use cases.
Computer vision is traditionally used for the purpose of automating image processing. It is all about automating the capture and processing of images with a heavy focus on image analysis. Basically, computer vision’s goal is not just to see things, but also to process the things that it sees and provide useful results based on the observations.
Machine vision, on the other hand, focuses on the application of computer vision in real-world interfaces, like a factory line. Machine vision is essentially a subcategory of computer vision. As an example, if you make use of computer vision in manufacturing, it would pretty much count as machine vision.
To sum it up, computer vision is used to describe pretty much any kind of technology in which a computer has the task of digitizing an image, processing the data it contains and performing some kind of action. The term machine vision is typically used when you are talking about the industrial and real-world applications of computer vision.