What Is a Warehouse Management System (WMS)?
A warehouse management system (WMS) is essentially a software system that brings visibility into the entire inventory of a business and helps it manage supply chain fulfillment operations all the way from the distribution center to the store shelf.
These warehouse management systems also make it possible for companies to maximize their labor and space utilization and equipment investments by co-ordinating and then optimizing the usage of resources and material flows for maximum efficiency.
Warehouse management systems are built for the purpose of supporting the needs of an entire global supply chain for various types of businesses - manufacturing businesses, distribution businesses, asset-intensive businesses, as well as service businesses.
In a world where customers want to buy anywhere, fulfill anywhere, and return anywhere, you need to have warehouse management software that optimizes your fulfillment capabilities.
Several enterprise software vendors sell warehouse management system software as either standalone products or as modules in comprehensive ERP suites. Some of these WMS vendors include:
- IBM
- Microsoft
- Oracle
- SAP
- Aptean
- ASCTrac
- Basware
- Fishbowl
- Manhattan Associates
%20(1).jpg)
What are the features of warehouse management systems?
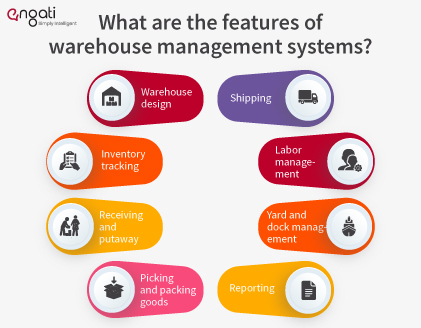
Warehouse design
This makes it possible for organizations to customize workflow and picking logic so that they can ensure that the warehouse is designed to optimize inventory allocation. The warehouse management system (WMS) can send bills of lading (B/L) ahead of the shipment, generate packing lists as well as invoices for the shipments and even send advance shipment notifications to the receivers. When using a courier service, there's a high probability that they use a WMS to optimize their shipment flow and keep things organized, especially if they offer same-day delivery.
Inventory tracking
This involves using advanced tracking and automatic identification and data capture(AIDC) systems which include RFID and barcode scanners to ensure that products being stored and transported can be located easily when they need to be moved.
Receiving and putaway
This makes inventory putaway and retrieval possible. There is usually pick-to-light or pick-to-voice technology being used to assist warehouse workers in locating goods.
Picking and packing goods
This includes zone picking, wave picking and batch picking. Warehouse workers can also make use of zoning and task interleaving functions to get the pick-and-pack work done in the most efficient and effective way possible.
Shipping
The warehouse management system (WMS) can send bills of lading (B/L) ahead of the shipment, generate packing lists as well as invoices for the shipments and even send advance shipment notifications to the receivers.
Labor management
The WMS aids warehouse managers in monitor workers' performance by using key performance indicators (KPIs) that show which employees are performing above the standards and which ones are falling below the standards.
Yard and dock management
This helps the truck drivers coming into a warehouse in locating the correct loading docks. Make use of more advanced yard and dock management makes cross-docking and other functions of inbound and outbound logistics.
Reporting
This assists the warehouse managers in analyzing and evaluating the performance of warehouse operations and identifying areas where improvements can be made.
What are the advantages of modern cloud-based warehouse management systems?
Cloud-based warehouse management systems can offer real-time visibility, scalability, and market reactivity. Here are some of the most significant advantages of cloud-based warehouse management systems.
Quicker implementation
Traditional on-premise warehouse management systems can take months to be implemented properly, while cloudd-based warehouse management systems can be deployed and implemented in just a few weeks, depending on how complex they are. This means that the organizations using cloud-based warehouse management systems can get to a quicker ROI in a much faster manner and can start reaping the benefits of their cloud-based warehouse management system much sooner instead of having to wait for months before they can start optimizing their warehouse management processes.
Fewer upgrade hassles
Cloud-based warehouse management systems deployed using the SaaS model have regularly scheduled upgrades in which the vendors handle all the updates and configurations themselves. This approach ensures that organizations are always using the latest version of the cloud-based WMS and spend the least amount of time and resources managing all the upgrades.
Lower costs
When your organization uses a cloud-based WMS, you do not need the installation of special hardware or software. You don’t need to have special IT administrators to handle and manage this hardware and software either. This means that you’ll have lower upfront costs (and sometimes lower ongoing costs too) when you use a cloud-based warehouse management system instead of an on-premise warehouse management system.
These warehouse management systems don’t even need equire customizations or modifications, which could be rather expensive for on-premises systems. Even upgrading on-premise systems can be a rather costly activity because it involves reinstalling and reconfiguring the software and, in certain situations, upgrading the hardware.
Rapid scalability
Cloud-based warehouse management systems can be scaled in a rather quick manner as the organizations that are using them grow and evolve. This is because when organizations grow, their supply chains become more complex. They’re also more flexible than on-premise warehouse management systems it is possible for the orgnanization to reconfigure them as its business requirements or market conditions change and shift.
How do warehouse management systems work with IoT?
Warehouse management systems can use connected devices and sensors in products and materials to aid organizations in shipping the correct quantity of products or materials at the right price to the right place at the right time. This becomes even easier when the internet of things (IoT) is brought into the picture.
IoT data can be integrated into the warehouse management system to help in managing the routing of the products from the pick up point to the place where they are delivered. Integrating these systems aids organizations in develop pull-based supply chains, rather than push-based ones. Pull-based supply chains are driven by demand from customers, which makes it possible for organizations to be more flexible and responsive. On the other hand, push-based supply chains are supply chains that are driven by long-term projections of customer demand.